Speaker: Kōzō Ue, washi paper craftsman
The Kuzu area has a history of washi paper making that goes back to ancient times.
About 1,400 years ago, the manufacturing method of washi paper was introduced to Japan by a Korean monk. It seems that washi paper was used for sutra copying in order to spread Buddhism. It is not clear when washi paper making started in Kuzu, but it seems that after the capital was relocated in 794 CE, it became known as a popular craft in the mountainous area of Yoshino.
In the middle of the Meiji era (1868-1912), 300 families, which made up about half the families of the Kuzu district, were making washi paper. As demand for washi paper has decreased since World War II, there are now only five washi paper workshops in the Kuzu area of Yoshino Town. Currently, half of these factories have no successors.
I think everyone knows that paper is made from plant material. However, I don’t think there are that many people who know in detail about what these plants are.
Generally, paper (*such as standard printing paper) that we use everyday are made of fibers (wood pulp) obtained by crushing up the trunks of trees (discarding the bark). Japanese washi paper, on the other hand, is characterized by using the outer “skin” (bark) layer of plants instead of the inner “trunk” part.
Washi paper is made from the “skin” of trees such as kozo, mitsumata, and ganpi.
The washi paper made in Yoshino is made from kozo, which is characterized by its long fiber strands and suppleness. Kozo is a deciduous shrub of the Moraceae family and is easy to grow and can be harvested every year.
For this article, I wanted to talk to Kōzō Ue, a 6th generation member of the Ue Washi Workshop, about how the skin of the kozo plant becomes paper.
On a winter’s day 1
Washi paper making begins in the deep cold of January with the harvesting of the kozo plant. Harvesting the branches one by one, it is manual work under a very cold winter sky.
“We can’t harvest it on rainy days, but we can on snowy days,” says Mr. Ue. Just imagining it makes me shiver.
Among the craftsmen of washi paper in Kuzu, there are now only two workshops (Ue Washi Workshop and Fukunishi Washi Workshop) who grow kozo themselves.
To harvest kozo, experienced people use a hoe, but amateurs like me can easily use scissors instead. However, since the branches of a mature tree are over 3 meters long, it can be difficult to handle for a beginner.
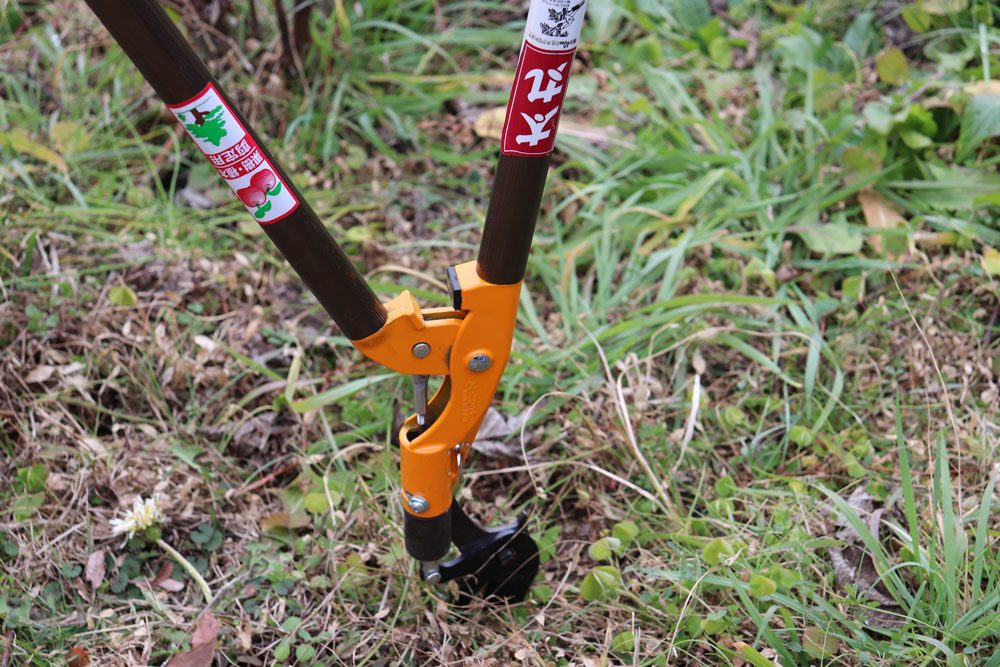
Thick branches are about 3cm in diameter, but these scissors can easily cut it without much effort.
The technique for harvesting is “diagonally from the root.”
Kozo grows to a large size within just one year, but since it does not grow again from places it has been cut, it needs to be harvested from the root to ensure that it will grow back properly. The reason for cutting it diagonally is to make the peeling process easier.
Kozo is a relatively easy-to-grow tree, but it is important to prevent it from being eaten by deer. Though not well-understood, it seems that deer saliva contains ingredients that are not good for kozo. The parts of that plant that deer have eaten will not grow and become weak. Therefore, the heavy labor of setting up fences and nets is necessary to protect the kozo from deer. For a long time in the past, Kuzu was an area that did not have deer, yet they started to appear about 15 years ago.
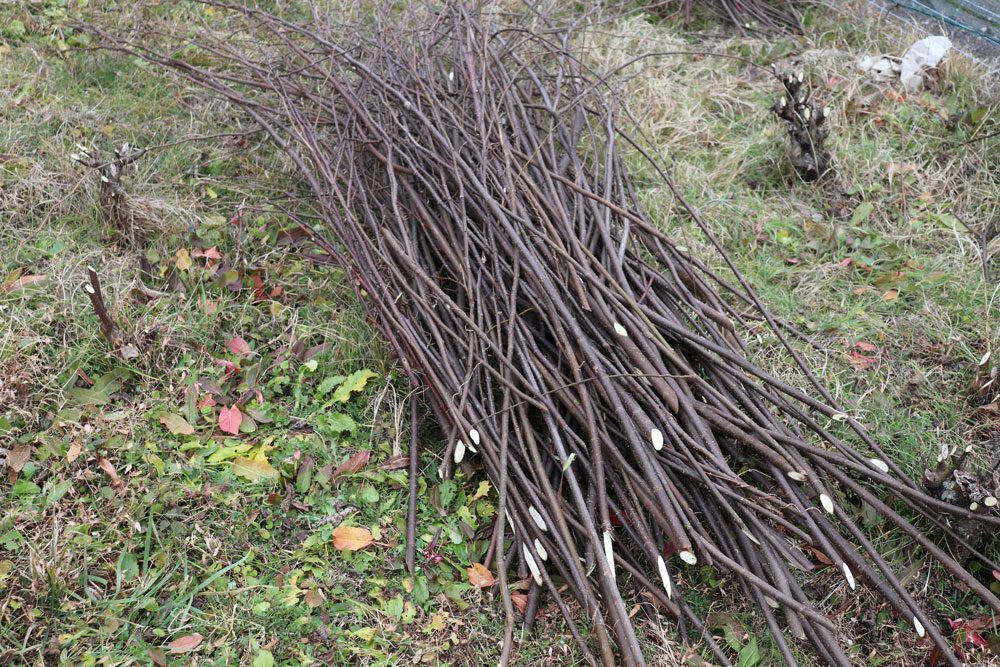
Branches after harvest
On a winter’s day 2
Cut off the finer branches and arrange them to a length of about 1.2 m.
On a winter’s day 3
Now it’s time to peel off the skin of the kozo. First, put the branches in a large steamer that has been used for over 10 years.
This steamer was made by a craftsman from Kuzu who has since passed away. Now, there are no other craftsmen here who can build such a steamer, so great care is taken when it is put to use. Hearing this, I felt that it is also important to preserve and hand down the skills required to make the tools that support this kind of work.
The kozo takes about 3 hours to steam. As the steamer operated, a slightly unique and sweet odor (like steaming sweet potatoes) spread throughout the room.
Opening time!
The sight of both steam and light was so beautiful that it made me stare. When cooled, the skin becomes hard and difficult to work with, so it is important to quickly peel it off while it is still warm.
The peeled off skin is called “kuroso“.
On the day of this task, 12 to 13 came to help out. Among the participants, there were people there who do this work every year and also first-time amateurs like me. There was also a 5th grade boy who has been participating for the past few years. Don’t underestimate even elementary school students. He did really good work.
He advised me not to pull the bark, but to remove the inner branch instead. I tried to copy his technique, but it took me a while to get the hang of it. I felt nice when I could finally pull it off. Meanwhile, Mr. Ue was peeling the kozo amazingly quickly and the work was completed in no time.
When I looked at the skin and branches side by side, I thought that the beautiful peeled branches were what must be used for making washi paper. However, it is only the brown skin that is used. In terms of proportion, it is only about 7% of the kozo harvested.
The remaining 93% of the branch was used as a fire starting material in the past, but nowadays there are no homes that use firewood so there is no use for it.
The peeled branches are a very beautiful pure white color. Since they contain a lot of water, mold will grow on them immediately if it is stored in an area with high humidity. However if they are dried well, they can be stored in it’s peeled form.
The leftover branches will definitely remain part of the process of making washi paper. This makes me wonder if there is any good way to use it.
<< If you would like to use this material, please contact us!>>
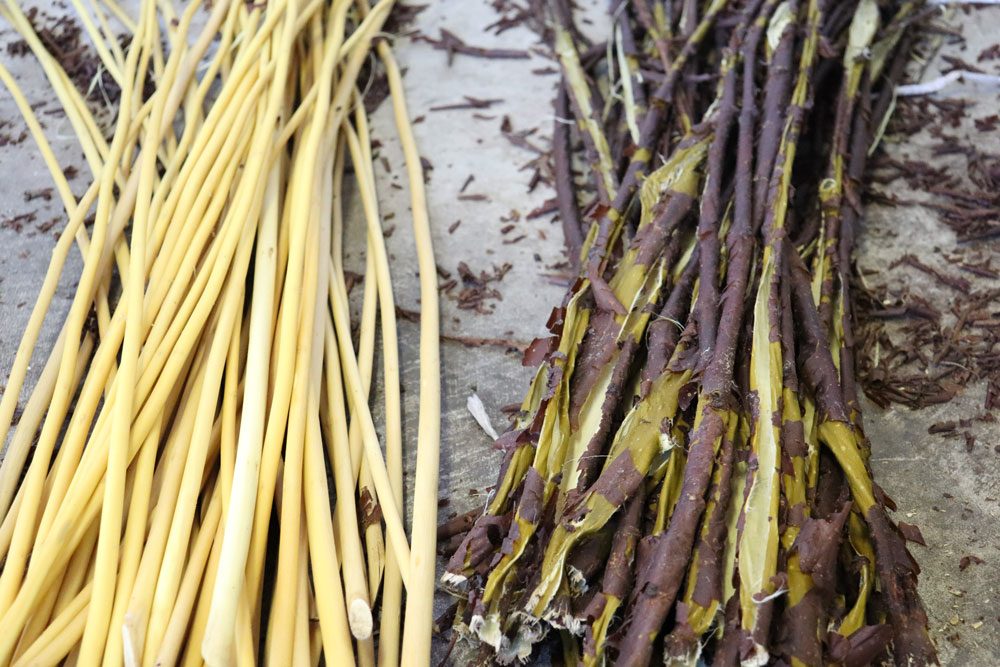
No matter how I look at it, the white branches seem like it should be the main ingredient.
The peeled skin will be left in the sun for several days until completely dry.
Even though it has taken a considerable amount of hard work to get to this point, the washi making process has still just begun.
Ue Washi Workshop
Address: 237-1 Minamiono, Yoshino-cho, Yoshino-gun, Nara 639-3437
TEL / FAX: +81-746-36-6134
HP:http://kuzunosato.jp/self/uewashi.html
Washi Making Experience
You can experience making washi paper at the Ue Washi Workshop.
* Please make a reservation 10 days in advance by TEL or FAX.
Kōzō Ue
Born in 1968.
Sixth generation washi craftsman of the Ue Washi Workshop
He started to make washi paper after graduating from high school.
He is aiming to be innovative in his washi paper-making, going beyond tradition.